Trade stacking in construction is a crucial issue that impacts project success. A construction site typically involves various trades, such as electricians, carpenters, HVACR technicians, drywall installers, painters, and heavy equipment operators. They all are working together to complete their tasks simultaneously in the same place.
Overlapping of trades can result in mistakes, delays, reduced productivity, and safety issues for construction projects. For the construction industry recognizing the seriousness of trade stacking is key to effective project planning and management.
In this blog, we will discuss the causes and impact of trade stacking in construction. We’ll provide actionable strategies to prevent these issues and improve project management.
What is Trade Stacking in Construction?
Trade stacking in construction is a scheduling work where many subcontractors are organized to work at the same region within the construction site. While it might seem like a good idea to speed up the project by having more on-site workers, it often leads to problems.
Overcrowding can create a chaotic environment, where workers interfere with each other. It tends to slow down the process of work and make it more cumbersome. It also increases the rate of accidents and brings down overall productivity standards within the workplace.
Trade stacking normally occurs due to changes in project scope, delays, or poor initial planning of the trade. Proper scheduling and coordination are important to avoid the downsides of having too many trades working in the same space simultaneously.
For example, one crew might be installing drywall while another is doing electrical work. It is beneficial in completing the project within a shorter time but requires close supervision. If not done right, it can cause uncertainties or mistakes.
Impacts of Trade Stacking in Construction Industry
Trade stacking in construction leads to several negative impacts:
1. Disruption and Delay Claims
Disruption and delay claims are common in construction projects when subcontractors face inefficiencies due to factors beyond their control. Disruption claims arise when work is completed less efficiently than planned. It leads to additional costs for labor, equipment, or delays. Projects may fall behind schedule, resulting in missed deadlines. It may affect the project's delivery date and may lead to disputes between the contractor and the client.
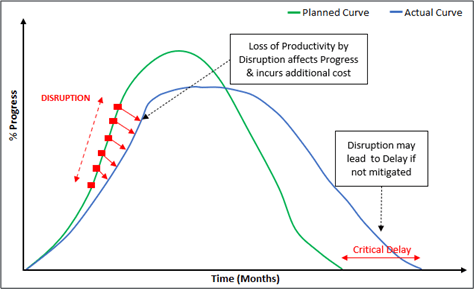
2. Safety Hazards
Overcrowding a worksite with multiple trades increases the risk of accidents. There are too many workers and their equipment on the job site and they may have to navigate around each other. It increases the risk of accidents, falls, or injuries. Safety hazards can lead to compliance issues with safety regulations, resulting in fines, increased insurance costs, and work stoppages.
You Must Also Read:- Wage Theft in Construction
3. Reduce Productivity
When multiple trades work in the same space at the same time, they often get in each other's way. It can cause delays, as workers have to wait for others to finish before they can start their tasks. These delays and interruptions can lead to mistakes or rework, as tasks might not be completed correctly the first time. As a result, the overall productivity on the site decreases, which can push the project timeline back and increase costs.
4. Overcrowded worksite
Construction sites are often busy with workers and machinery. When a site becomes overcrowded, it can create logistical challenges, such as insufficient space for tools and materials. It causes disorganization and inefficiency. Overcrowding also makes it harder to keep the work environment clean and orderly.
5. Increased Costs
All these factors discussed above increase the cost of construction projects. Delays and disruptions can extend the project timeline, requiring more labor and resources. It includes direct costs such as labor and materials, as well as indirect costs such as legal fees and potential penalties. It makes the project more expensive than originally planned.
Causes of Trade Stacking in Construction
Trade stacking can significantly disrupt a construction project leading to various issues that we already discussed above. Several key factors contribute to trade stacking on construction sites. Here are some of them:
1. Poor Management and Scheduling
Effective project management and scheduling are necessary to prevent trade stacking. If project managers don’t create and plan realistic schedules or sequence tasks properly, multiple subcontractors may be assigned to the same area. It causes overcrowding, competition for space and resources, and decreased productivity.
8. Project Acceleration
Project acceleration speeds up construction to meet tight deadlines or recover from delays. Trade stacking can happen when a client requests an earlier delivery date. General contractors or project managers might fast-track the schedule to meet this new deadline by stacking trades to work together or with overlapping tasks.
8. Delays in Previous Tasks
Delays in earlier tasks can have a cascading effect on the entire project schedule. When you delay the initial tasks, subsequent workers are forced to work in a tight timeframe. If the structure of a building is delayed, the scheduled electrical and plumbing work will overlap, causing congestion and inefficiencies. If one trade falls behind, the next scheduled trades may have to work together to stay on track.
9. Limited Workspaces
Construction sites in urban areas or small projects often need more space available for workers and materials. When several trades work in the same confined area, it becomes challenging to maintain productivity and safety standards.
How to Avoid Trade Stacking in Construction?
Trade stacking often leads to stress and distractions that can cause workers to overlook safety and reduce the quality of their work. To avoid trade stacking, you can try these strategies:
1. Manage the Schedule
Project managers start by creating a detailed project schedule that outlines all construction phases and activities. They break down the work into tasks, estimate the durations, and organize all the project tasks. Construction scheduling involves resource management, allocation of assets, task durations, deadlines, budgets, and other related costs. Proper scheduling of the construction project helps minimize trade stacking.
2. Consider Prefabrication
Prefabrication avoids trade stacking by allowing builders to assemble components off-site. Workers construct parts like walls and floors in a factory before bringing them to the construction site. When these pre-assembled parts arrive, they require less work on-site. It keeps the site less crowded and prevents multiple workers from working in the same area at the same time. As a result, employers can work without interfering with each other.
3. Manage Uncertainty
Construction projects rarely follow the original plan perfectly. General contractors can manage these uncertainties using workforce management software like Kwant. Kwant helps identify bottlenecks, compare scheduled vs. actual manpower on-site, and provide heatmaps of trades by zone. It also uses advanced analytics to solve problems proactively. Kwant makes it easier to adjust schedules and avoid conflicts.
You Must Also Read:- Wrap-up Insurance
4. Use Construction Workforce Management Software
Utilize smart technology and construction management software Kwant to track attendance and monitor the workforce in real time. Kwant assists general contractors in determining whether they are over-allocating the workforce to a project. Additionally, it optimizes resource allocation, predicts labor needs, enhances workforce planning, and tracks attendance in real-time.
Use Kwant AI to Minimize Trade Stacking in Construction
Kwant is a leading workforce management & safety platform that assists general contractors to track and manage the workforce. Kwant helps construction speed up with IoT hardware and applications for safety & performance tracking in real-time.
Similarly, Kwant helps minimize trade stacking through several innovative approaches:
- Real-Time Workforce Tracking: Kwant uses smart wearables and sensors to track the location and movement of workers and trade partners on-site. The real-time data allows general contractors to monitor where each trade works and identify potential overlaps before they become problematic.
- Scheduling: With Kwant, the construction industry can upload and refine schedules in real time. It helps identify high-risk areas, automate short-term planning, and improve overall progress tracking. It also reduces trade stacking by increasing schedule reliability and minimizing delays, leading to a smoother project experience.
- Resource Optimization: The AI-driven insights from Kwant help optimize the allocation of resources, including labor, materials, and equipment. Kwant allows teams to monitor the usage and location of equipment in real-time, helping them identify assets that remained ideal for too long. It catch the shipping delays, and reduce material wastes.
- Automated Reporting: Kwant generates automated reports that provide insights into workforce productivity, site conditions, and potential risks. You can export all the data created and stored in the Kwant platform in one click. These reports help general contractors make informed decisions to minimize trade stacking and improve overall project efficiency.
Optimize Your Construction Workflow With Kwant
Trade stacking can be a problem in your construction project because it creates inefficiencies which can slow down the project and increase its cost. Kwant solves such problems by offering real-time workforce monitoring, scheduling, and resource management. These tools prevent overlaps between trades and keep your project on track.
Don’t let inefficiencies slow down your project’s success. Take control with Kwant’s easy-to-use platform. Contact us to request a demo and learn more about the capabilities of Kwant and how it can enhance construction management and project success.