Your brief enlightenment on construction safety; the issues presented and the solution brought to you by Kwant.
The worst possible day for a safety manager is when an enterprising employee goes to an unauthorized zone and gets hurt. Even though there were protocols in place to prevent this very scenario, the worker takes a shortcut as the project was delayed and the pressure to finish was tremendous.
This cost the company not only in lost productivity, wages and decreased morale but also increase in insurance premiums, legal and administrative expenses.
.png)
Safety in the construction industry has improved a great deal compared to the past but is it satisfactory enough? There were 1083 fatal injuries (971 in Construction, 112 in Mining) and 208,000 nonfatal injuries in the year 2017 alone and 60% of fatalities can be categorized by falls, struck by an object, electrocution, and caught-in/between objects or commonly known as the fatal four.
.png)
The Cost of “Safety”
Industry perspective:
Prevention is better than cure is the mantra that companies should abide by and it is understandable when you look at the cost of not having a rigorous safety program.
The direct cost for the construction firms in the US is around $10 billion, an average of $39,000 for an injury and the loss of productivity for the industry is estimated to be around 4.8 million days in a single year.
When you consider the indirect costs like increase in premiums, loss of morale, time, efficiency etc the costs mounts upto two to four times the direct costs.
Insurance perspective:
Insurance is the fall back plan for accidents that your safety program failed to prevent and one way it impacts the profit margin is by EMR or Experience Modification Rate.
EMR is the measure by which insurance companies determine the past costs and future chances of risk. An EMR of 1.0 means your company's workers' compensation claims experience is no better or worse than your industry.
Higher the EMR more the premium you pay. One of the factors that affect EMR is the frequency of claims. A company with one big claim would be penalized less severely that a company with multiple small claims because a higher accident frequency indicates a lax safety culture and a high risk of future accidents.
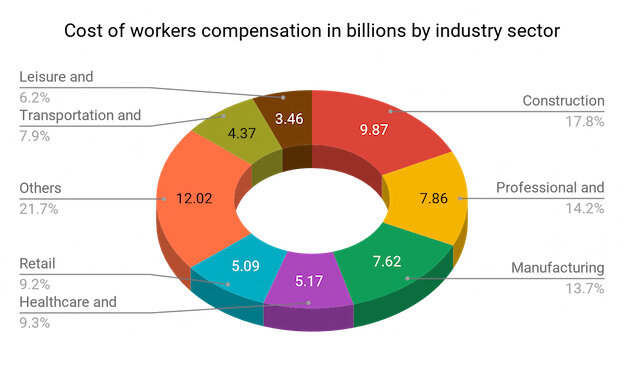
How to Improve Safety?
Real time insights:
One of the important factors in limiting the severity of a safety incident is to provide adequate and fast response to the persons affected. To be able to do that, the safety manager must be aware of safety incidents as soon as it occurs.
With the advancements in IoT, Kwant has developed a system which tracks the location of the workers in real time and sends notification when a person enters an unsafe zone.
Also in case of an emergency, the worker double taps a button on his badge, which sends a safety alert containing the name of worker and his current location to the project team. This has reduced the response times by 92% and also has enabled the project team to have real time visibility on job site.
Proactive decision rather than reactive:-
Another facet of the issue is how to reduce the frequency of incidents. Currently, the insights or intelligence generated in a project is not implemented elsewhere. This leads to a the same scenario which could have been prevented being repeated time and time again.
One way we are trying to overcome the problem is by using the real time insights and machine learning to decipher patterns involving safety incidents and eventually come up with a way to predict them before they occur.
The insights not only transcends projects but also can be used on an enterprise level to improve the safety policies which in turn create safer worksites for the employees.
Proactive decisions have already shown ROIs of avoiding more than 25% safety incidents. For a large construction company, that's 50 incidents in average. With the average cost of $39,000, that's a saving of millions of dollars. ( For a company of size Permira, it will be 20 incidents, thats a savings of $0.7M/year)
Systemic and integrated measures:
In a job site today the environment is constantly changing and when you look at it from a safety perspective, a job site that is safe today doesn’t guarantee it safe tomorrow. For example, let's look at the following scenario, There are slightly uneven steps in the middle of a staircase
- For a worker climbing it there is a very low probability of trip hazard
- A worker being late for work is rushing up the stairs and because his attention is divided the risk of tripping also increases.
- Similarly, a worker carrying a load and is moving up the steps in a faster pace. The trip hazard has now changed into a fall hazard with a high probability due to an uneven center of mass.
Insurers are excited about introducing innovative ways for data driven underwriting. Insurers are even interested in offering discounts to Construction companies of upto 2% in insurance cost if they can adopt advanced technologies to mitigate risk.
That's an additional 2% in profits and operating capital for construction companies. However for that,we have to change the way we see safety at job sites.
We have currently improved safety for single factor incidents but when more than one factor is involved i.e when the safety environment becomes dynamic we are still lacking.
This can only be improved when safety data is constantly collected and we move to implementing systemic and integrated measures towards safety rather than static and standalone measures. This is especially true when you have things you can’t control, like the safety training and compliance of subcontractors, unforeseen situations.