Kwant Implements Lean Planning
Kwant applies Lean planning principles using the Last Planner System, in that we start with the Master Schedule, create a weekly work plan and lookahead schedule, and provide PPC and report analytics for continuous learning.
Kwant. tracks and improves on PPC’s, wastes, and constraints in a series of reports that can be used to continually improve processes. As an owner or GC, we enable you to add invite subcontractors to collaborate, add and edit activities on 2-week, 4-week, and 6- week lookahead schedules, , and create a weekly work plan using Calendar and Gantt view.
You can add and edit tasks and constraints, and change the status of any planned task, as well as add wastes and generate PPC reports.
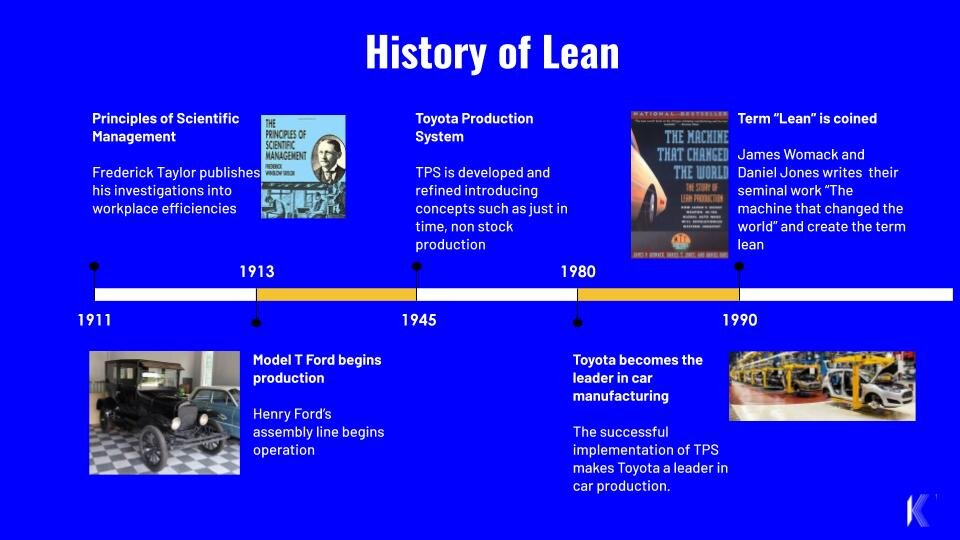
Background on Lean Manufacturing
Lean Planning evolved in the late 1890s, when the US had primarily been focusing on the development of machinery and large scale processes. Previous focus was made on the ordering of one discrete process to another.
Little attention was paid to what happened between processes, how those processes were arranged and functioned within a system, and how each worker went about each task.
Frederick Taylor was the first to look at individual processes and work methods by examining the time workers spent on each activity and creating standardized work processes.
He referred to these processes as the Scientific Work Method, and published papers on his findings in 1911. Only a few years later, in 1913, Henry Ford, developed a method to critically arrange a continuous system of people, machines, tooling, and products to manufacture the Model T automobile.
His methods were later critiqued for taking advantage of the current economic climate. Yet, the Toyota Motor Company, built on the Ford production system and dubbed their new approach the Toyota Production System.
They recognized the central role of inventory and the processing of inventory “just in time” for the next operation. Their focus on inventory and team development led them to be clear leaders in car manufacturing and development.
The term “Lean manufacturing” was officially defined in the 1990s in John Krafciks and James Womack’s book on “The Machine That Changed The World.” This book provides a review of the automobile manufacturing history, and compares Japanese, American, and European automotive assembly plants.
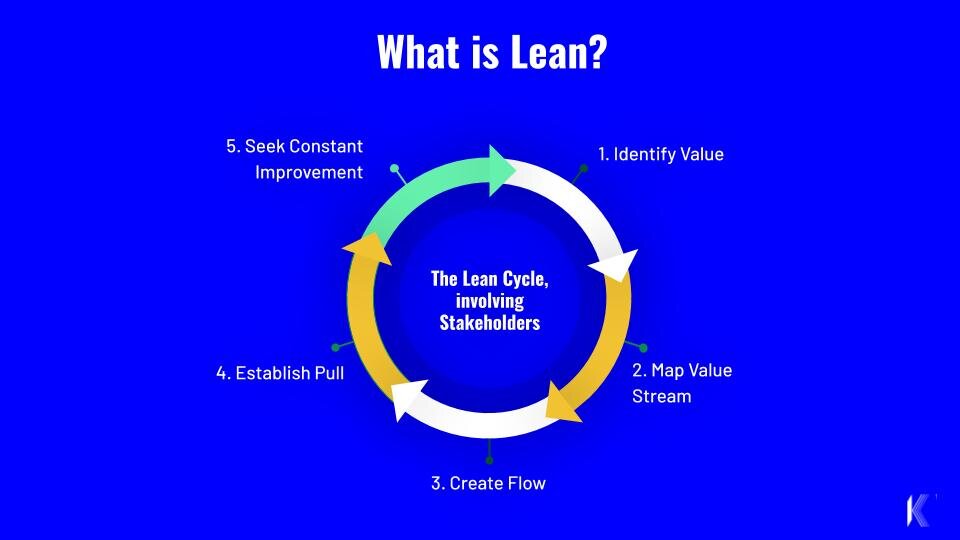
Lean Defined
Lean Planning, or Lean, used today derives from the Lean Manufacturing principles of the 1900s. Lean is not a software, and it is not a technology. Lean is a philosophical approach to improve your process, reduce waste, and increase accountability among your workforce.
The first step in Lean Planning is the value creation, which brings together all stakeholders including the owner, architect, engineers, general contractor, subcontractors, and suppliers.
The project team not only delivers what the client wants in their project plans and specifications, but they provide advice and shape expectations throughout the project.
This process is then followed by defining your value stream, including the necessary labor, information, equipment and materials for each planning activity throughout your project.
In the pre-construction phase, and as you begin your work, you identify and eliminate wastes in your planned processes, which are defined as anything not necessary to produce the product or service.
Your goal is to create a continuous, uninterrupted workflow that is reliable and predictable. In order to achieve this, you need clear communication between all parties.
When one part of the project gets behind or ahead of schedule, it is essential to let everyone know so that adjustments can be made to avoid the wastes of waiting, motion, and excess inventory.
Starting with each planning milestone, each team works backward to set out the tasks that efficiently lead toward task completion. The belief is that it is possible and necessary to continuously improve processes and eliminate waste in order to achieve continuous improvement on future projects.

The Last Planner System (LPS)
The Last Planner System (LPS) is a collaborative planning process that involves trade foremen or design team leaders in planning in greater and greater detail as the time for the work to be done gets closer.
The Last Planner System, or LPS, comprises four planning stages:
- The Master Schedule summarizes all the work that should be done in abstract terms.
- The Phase Schedule defines project phases and is used to coordinate actions that extend beyond the lookahead window. Phase schedules provide more details regarding what should be done and when.
- The Lookahead Planning presents a time frame of roughly two to six weeks and is the stage where tasks are broken down and made ready.
- The Commitment Planning comprises the most detailed planning stage that results in commitments to deliver the work that was placed on the Weekly Work Plan (WWP)
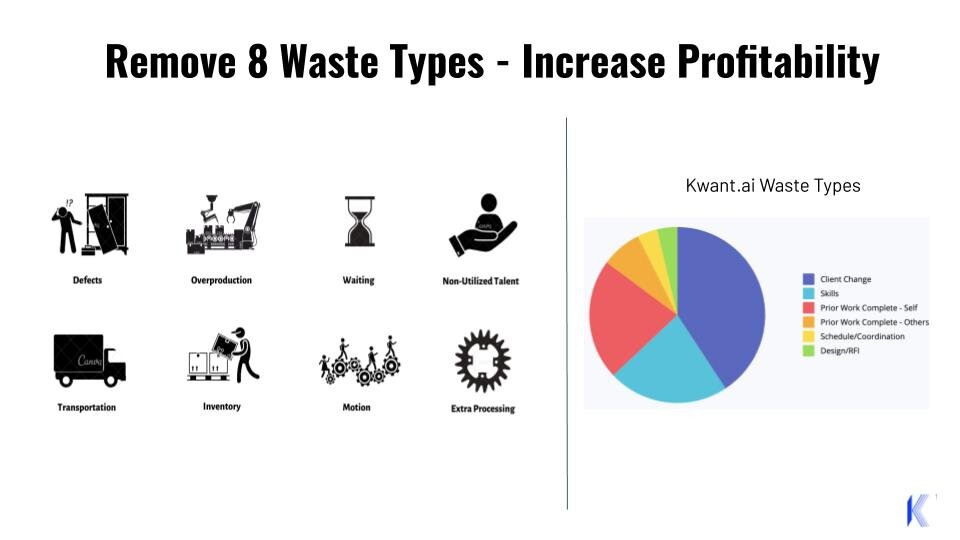
Reduce Waste
The primary goal of Lean planning is to identify and eliminate 8 major types of wastes:
- Defects: Anything that is not done correctly the first time, resulting in rework that wastes time and materials.
- Overproduction: When a task is completed earlier than scheduled or before the next task in the process can be started.
- Waiting: When the necessary materials needed for the work to be completed have not been delivered or the prerequisite prior task has not been completed.
- Not Utilizing Talent: When the right person is not matched to the right job, and their talent, skills, and knowledge go to waste.
- Transport: When materials, equipment, or workers are moved to a job site before they are needed.
- Inventory: Materials that are not immediately needed are considered excess inventory. They tie up budget, require storage, and often degrade when not used.
- Motion: Movement that is not necessary, such as the distance between workers and tools or materials.
- Over Processing: When features or activities are added that have no value to the client. Ironically, this often occurs when taking steps to eliminate the other types of waste.
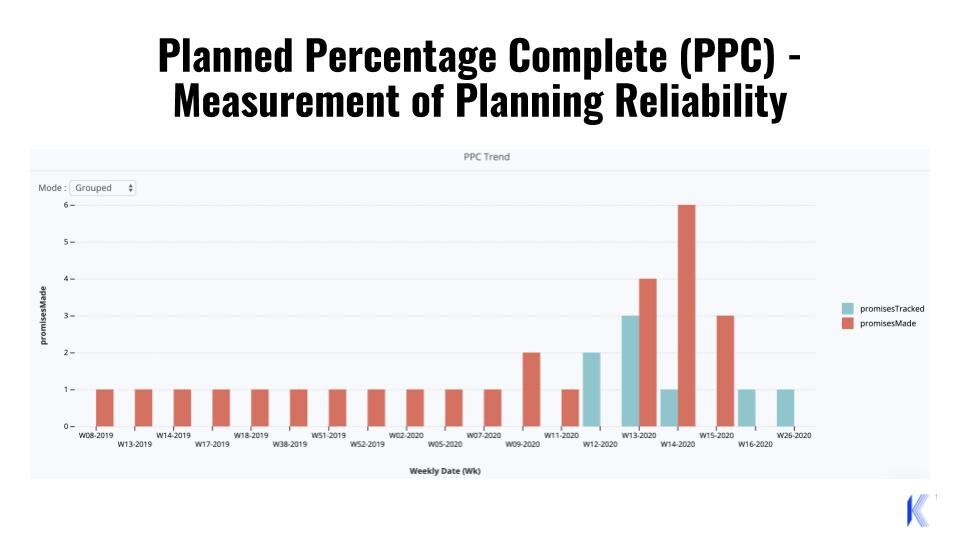
Increase Accountability
One benefit of lean planning is the creation of accountability among the workforce. We measure the level of planning reliability among the workforce using planned percentage complete (or PPC reports). We track what promise was made vs. what promise has been completed.
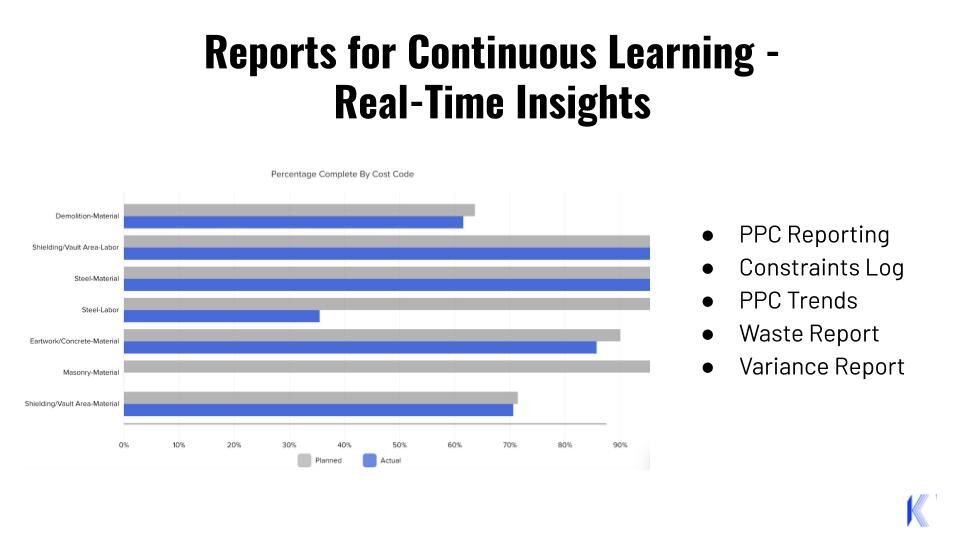
Remove Bottlenecks - Reporting
Our other focus is on anticipating tasks and removing constraints to make activities ready for implementation. Theory of Constraints (or TOC) focuses on system improvement, which we define as a series of interdependent processes.
The constraint in a group of interdependent links is the weak link. The performance of the entire chain is limited by the strength of the weakest link.
Constraints range in anything from design to technical, economic, management, time, legal, social, and environmental constraints. Kwant provides constraint, waste, and PPC report analytics on customizable date rates and crews for continuous learning.