Modular construction is the bridging of the factory and the field, relying on manufacturing-style production systems and pre-fabricated components that are produced off-site with minimal on-site assembly [1].
Places like Scandinavia and Japan previously experienced labor shortages, and their response to the labor shortages was modular construction [2].
While modular construction currently comprises 3% of the US residential market [3], we have to change the current approach because similar labor shortages are now occurring here in the US.
Drivers of Cost and Productivity
The June 2019 McKinsey report on modular construction shows that modular construction can lead to a 20-50% accelerated schedule in development. One of the primary drivers of an accelerated schedule includes parallel on-site and off-site production.
The lean off-site manufacturing process can be significantly faster than the onsite building process due to the enclosed and controlled factory environment, the ability to create repeatable processes, as well as increased levels of automation [4].
These same benefits result in cost savings with digitization and automation, leading to potentially greater volumes of production with greater investment in design and BIM work heavily invested to mitigate risk upfront.
These benefits are being realized in places like China during the recent Coronavirus outbreak where 2 hospital buildings with approximately 1,000 beds each were constructed in 10 days [5].
These blueprints were used during the SARS outbreak in China in 2003, in which a 1,000 bed facility was constructed within a week [6]. We are starting to see things like 3-D printing of homes on Mars, which benefit from standardization and repeatable processes with thermal considerations [7].
The Everyday Benefits of Modular Construction
The everyday benefits, including improved sustainability, significant cost savings, improved safety, and greater precision on-site, are being realized on a large scale, from the development of a daycare center at MIT in Cambridge, MA [8], to the construction of 850 bathroom units at a residence hall at the University of Michigan [9].
Buildings greater than 30 stories tall are already being built in places like the US, UK, and Singapore [10, 11, 12]. For example, Autodesk worked with modular home manufacturers, Factory OS and Blok to construct a 5-story building on the west coast in 6 days [13].
Emerging Markets for Modular Construction
The emerging market includes companies like Full Stack Modular [14][ and Katerra [15] that are particularly recognized for providing full end-to-end services from the design and architecture to material supplier and manufacturer, and finally to contracting and project management services.
Scandinavia-based Skanka and IKEA are partners in a company called BoKlok, where they have produced about 1,200 affordable, modular homes in the UK and Scandanavian countries [16].
General contractors like Kitchell [17], Mortenson [18], and DPR [19] have adopted structural frame fabrication and large scale production of hotel modular units, and are largely driven by the benefits of accelerated schedules, cost savings, and, even in some cases, by the sudden change in standardization of building codes.
In a survey of industry professionals on the benefits and challenges of modular construction, reported in a recent edition of the Dodge Report of 2019, modular contractors were most likely to realize the benefits of waste reduction and reduced safety incidents.
Alternatively, the greatest barrier to modular construction was the approval and acceptance of modular construction by owners and the availability of modular component manufacturers [20].
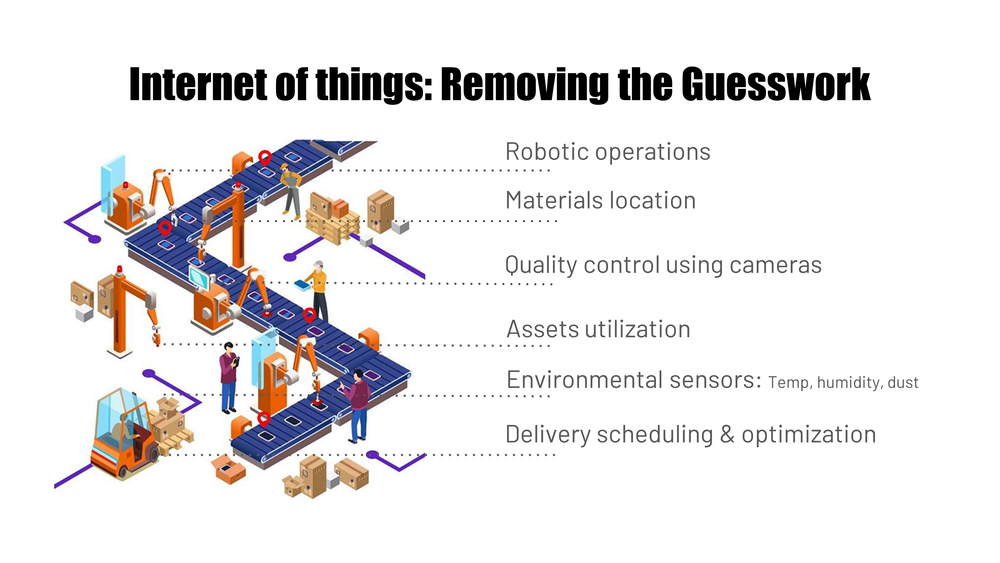
IoT Technology for Modular Construction
One of the drivers of improved cost and productivity in modular construction is the rise of new digital technology. IoT devices that are collecting data using sensor technology are aggregated in the cloud and used to make data-informed decisions. Iot devices like the Smart Watch, Nest thermostat, and self-driving cars are everywhere and they are only expected to grow to 50 Billion devices by 2023 [21].
IoT is being used in the modular manufacturing process to inform on such things as materials location, quality control, assets utilization, environmental variables such as temperature, humidity, and dust, and delivery scheduling and optimization (Exhibit 1) [22]. Kwant 2.0 already uses Low-Powered Wide Area Range (LPWAN) sensors to inform on things such as planned versus actual areas of work, the amount of time spent in high-risk areas in the field, and materials status [23].
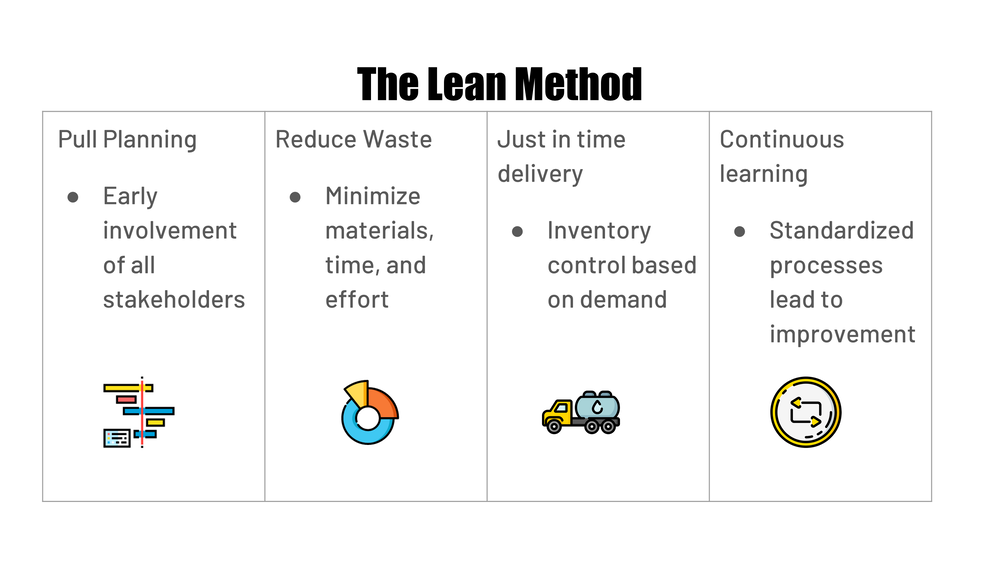
- Field Transformation Using 3D Models
The digital twin concept capitalizes on IoT and camera technology to create virtual simulations of physical attributes, including the factory, plant, product, and components. These IoT sensors are used to predict failures, enable remote commissioning and diagnostics, and inform on decision-making related to future products [24]. For example, in the preconstruction phase, clash detection has enabled us to resolve conflict on the digital twin of a building [25]. The 4D collaboration and 5D estimates have become really popular in order to coordinate among different trades and have a highly accurate budget of your project [26]. In the construction phase, using reality capture technologies, we are able to detect deviation from the design immediately and capture work-in-place for faster payments. Materials are tracked from procurement to delivery and installed using sensors, and productivity rates can be optimized by analyzing labor hours.
In the same way that the digital twin has been used historically in manufacturing such as the development of cars to customize features through virtual representations, which are then converted into physical objects. Similarly, construction is similarly using digital twin concepts using 3-D models. Modular particularly capitalizes on lean principles because it necessitates early involvement of all of the stakeholders. Because you are organizing how the building is going to be both manufactured and constructed, it is critical to have a coordinated effort in order to do delivery, preconstruction planning, and the integration of schedules between traditional construction and the modular production. That integration, the pull planning gives you the opportunity to save time and money.
- Real-Time Data Analytics for Cost Savings
Kwant software fully empowers you using 5D BIM and Lean in the modular design and construction process [27]. We have integrations with best-in-breed solutions with software like Procore [28], Primavera, Microsoft Project, and Autodesk [29]. Kwant uses real-time data that is collected in the field and this data can be collected using IoT technology in the form of Smart Badges, material tags, and mobile applications [30]. Kwant improves safety by sending an instant alert if there is a safety incident and reducing the response time in order to make sure our tradespeople get home safely. Material can be tracked on the job site using material sensors and RFID tags on high value items.
As an example, on one of our current projects, we saved Marlbro Construction $50,000 per month by identifying out-of-sequence work using Smart Badge and wearable technology. This is the case where we were able to see on our actionable online dashboard that prioritizes high-risk activities, zones, and trades so that we can take proactive actions. Using IoT technology you are able to improve location awareness which in turn improves productivity. For example, you are able to compare the scheduled area versus time spent using tools in the field. You can optimize materials and storage locations, and identify out-of-sequence work. In our recent project, we were able to understand that the total tool time comprised 53% of total man-hours on the project. The contractor was better able to optimize the location of material and improve productivity by changing locations and reducing travel time [31].
Conclusions
The construction industry is moving toward standardization and automation using 4D and 5D BIM, Lean Planning, and such things as IoT technologies. Modular construction currently comprises 3% of the US residential market, and will continue to grow as labor shortages increase across the country. Kwant is a safety- and productivity-driven IoT firm for workforce analytics and material and equipment tracking. We partner with construction global leaders like DPR, Mortenson, Haskell, and Delta, and are on projects worth $4-5 billion dollars. We have over 700 sensors on-site for workforce tracking and analytics, and we are moving toward automated tracking technology using material and equipment tracking features. We integrate with best-in-brand software including Procore, P6, Microsoft Project, and Autodesk, including BIM 360, to multiply your favorite project management capabilities. Contact Kelsey Poinsatte-Jones, Head of Growth at Kwant at kelsey@kwant with additional comments or questions.